Understanding the Timeline: How Long Does It Take to Create a Plastic Medical Mold?
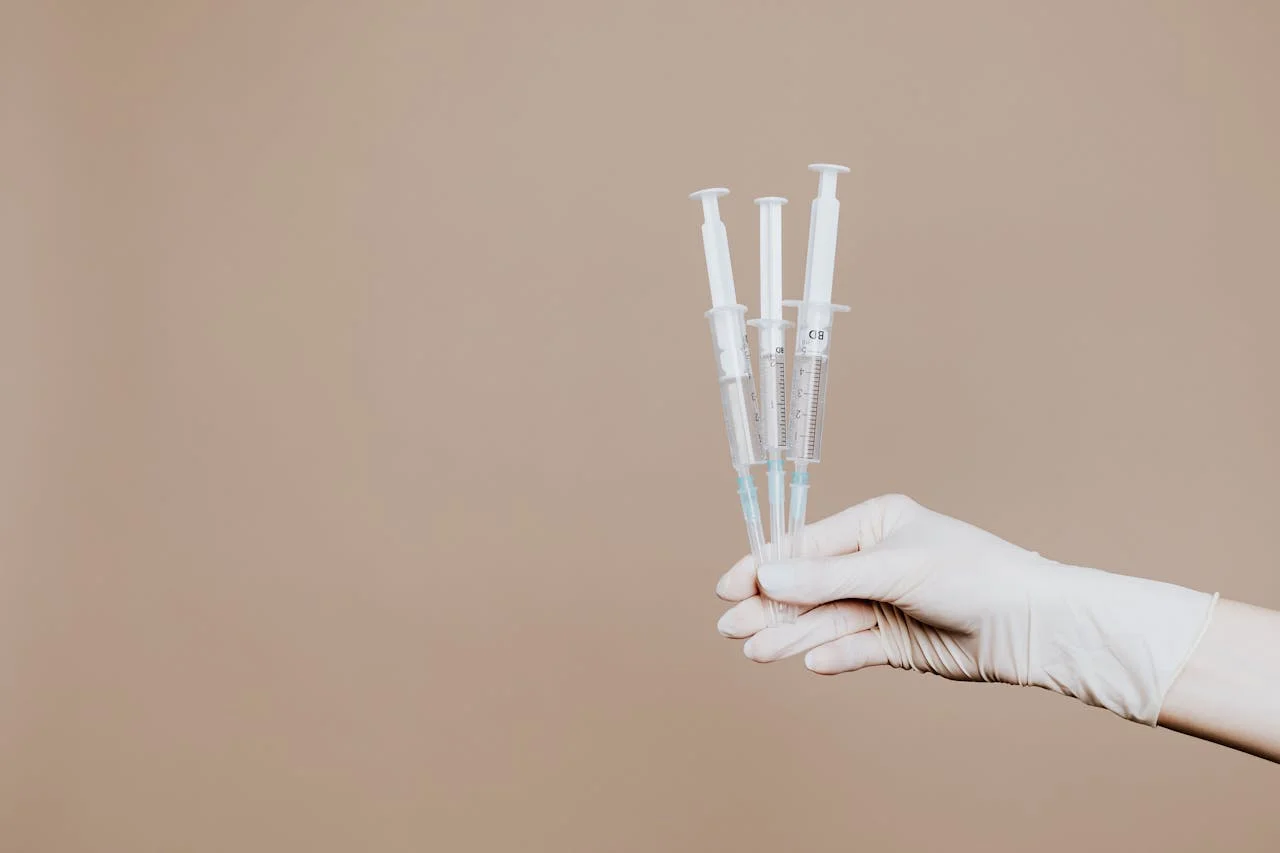
In the realm of medical device plastic molding, precision and efficiency are paramount. From concept to production, every step in the process plays a crucial role in delivering high-quality medical injection molding. Central to this process is the creation of plastic medical molds, which determine the final shape and specifications of the medical devices. Understanding the timeline involved in making these molds is essential for managing expectations and ensuring timely delivery of medical devices to market.
Contents
1. Initial Design Phase (1-2 Weeks):
The journey begins with the conceptualization and design of the medical device. During this phase, engineers and designers collaborate to create detailed drawings and specifications for the plastic mold. Factors such as material selection, part geometry, and manufacturing requirements are carefully considered to optimize the design for medical injection molding.
2. Mold Fabrication (2-4 Weeks):
Once the design is finalized, the next step is to fabricate the plastic mold. This process involves precision machining or 3D printing techniques to create the mold cavity and core. The timeline for mold fabrication can vary depending on factors such as complexity, size, and the availability of resources. Advanced technologies like computer numerical control (CNC) machining and additive manufacturing have significantly reduced the lead time for mold fabrication, allowing for faster turnaround times.
3. Mold Testing and Validation (1-2 Weeks):
Before mass production can begin, the newly fabricated mold undergoes rigorous testing and validation processes. This ensures that the mold meets the exact specifications required for medical injection molding. Testing may include trial runs with prototype materials, dimensional inspections, and performance evaluations. Any discrepancies or issues identified during this phase are addressed promptly to ensure the quality and functionality of the mold.
4. Production Setup (1-2 Weeks):
With the mold successfully tested and validated, the production setup phase commences. This involves preparing the injection molding machine, selecting the appropriate materials, and fine-tuning process parameters such as temperature, pressure, and cycle time. Additionally, quality control measures are put in place to monitor and maintain consistency throughout the manufacturing process.
5. Mass Production (Ongoing):
Once the production setup is complete, mass production of the medical devices can begin. The plastic mold is used to inject molten material into the cavity, which then solidifies to form the desired shape. This phase continues until the required quantity of medical devices is produced, with quality checks performed regularly to ensure compliance with regulatory standards and specifications.
Additional Information on Medical Injection Moulding:
Medical injection moulding plays a critical role in the production of a wide range of medical devices, including syringes, catheters, implants, and diagnostic equipment. The process involves injecting molten plastic material into a specially designed mold cavity under high pressure, allowing for the rapid and precise fabrication of complex geometries with tight tolerances.
Advantages of Medical Injection Moulding:
- Precision and Consistency: Injection moulding offers unmatched precision and repeatability, ensuring uniformity and consistency in the final product. This is particularly important in medical applications where even minor variations can have significant consequences.
- Complex Geometry: The versatility of injection moulding allows for the production of intricate and complex part geometries that would be difficult or impossible to achieve with other manufacturing methods. This opens up possibilities for innovative designs and functionalities in medical devices.
- Cost-Effectiveness: While the initial setup costs for injection moulding can be higher compared to other manufacturing processes, the economies of scale achieved through mass production result in lower per-unit costs over time. This makes injection moulding an attractive option for high-volume production of medical devices.
- Material Selection: Injection moulding supports a wide range of materials suitable for medical applications, including thermoplastics, elastomers, and bioresorbable polymers. Manufacturers can choose materials with specific properties such as biocompatibility, sterilizability, and transparency to meet the requirements of various medical devices.
Challenges and Considerations:
- Regulatory Compliance: The medical device industry is highly regulated, with stringent requirements for product safety, efficacy, and quality assurance. Manufacturers must ensure compliance with standards such as ISO 13485 and FDA regulations throughout the injection moulding process.
- Material Compatibility: Selecting the appropriate material for medical injection moulding is crucial to ensure compatibility with the intended application and regulatory requirements. Factors such as biocompatibility, chemical resistance, and sterilization methods must be carefully considered during material selection.
- Tooling and Maintenance: The quality and longevity of the plastic mould directly impact the quality and consistency of the final product. Proper maintenance and periodic inspection of the mould are essential to prevent defects, prolong tool life, and minimize production downtime.
- Risk Management: Injection moulding involves inherent risks such as material degradation, tool wear, and process variability. Manufacturers must implement robust risk management strategies to identify, mitigate, and monitor potential risks throughout the manufacturing process.
Conclusion:
Medical injection moulding continues to revolutionize the healthcare industry by enabling the efficient production of high-quality, cost-effective medical devices. By leveraging advanced technologies, materials, and manufacturing processes. Manufacturers can meet the growing demand for innovative healthcare solutions while ensuring compliance with regulatory standards and patient safety. As the field of medical injection moulding continues to evolve, collaboration between manufacturers, regulators, and healthcare professionals will be essential to drive advancements and address emerging challenges in the dynamic landscape of medical device manufacturing.
Also Read: Health Redefined: IV Therapy and Spas Transform Healthcare Experiences