Understanding Medical Injection Molding: A Crucial Process in Medical Device Manufacturing
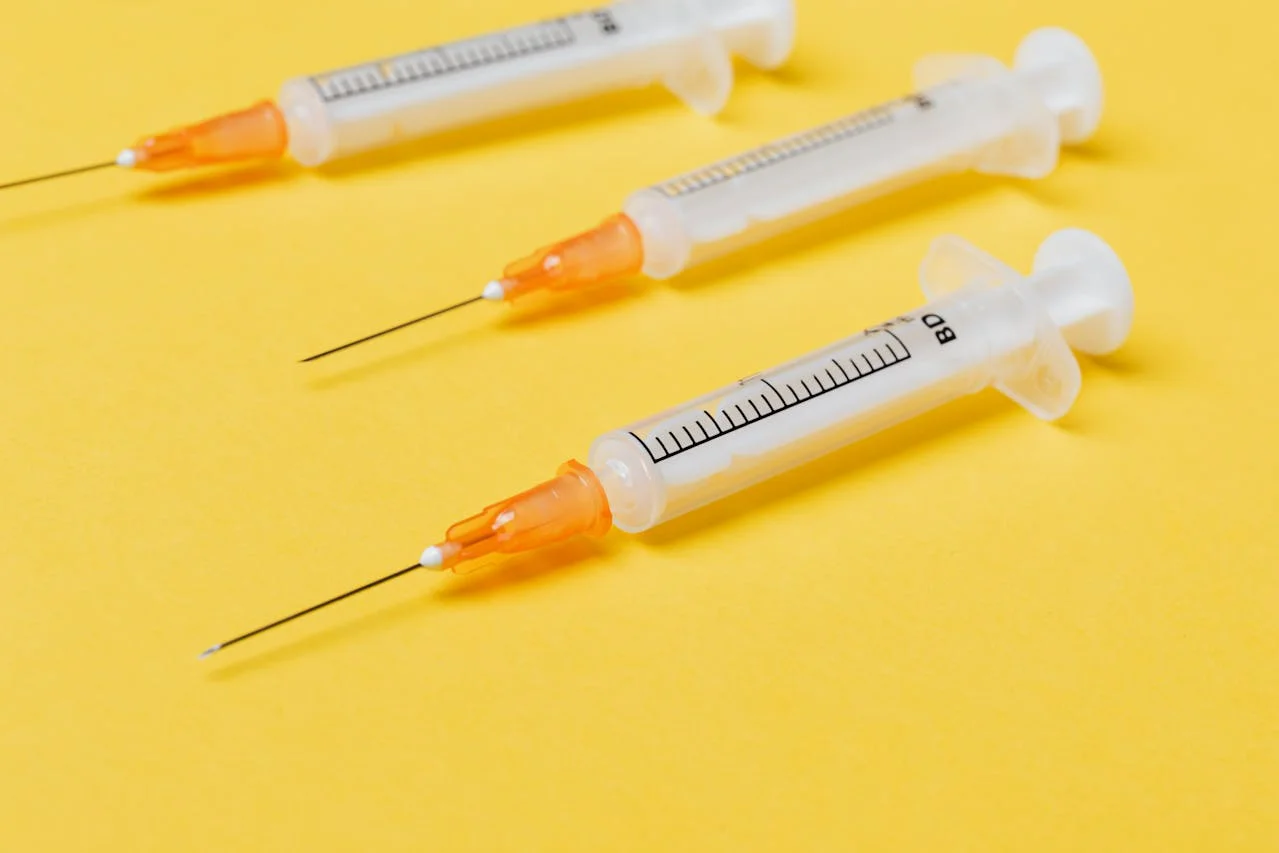
Medical injection molding, also known as medical device plastic molding, is a pivotal process in the production of various medical devices. This process ranges from intricate components to essential tools used in healthcare settings. Moreover, medical injection molding plays a significant role in ensuring the reliability, precision, and safety of medical equipment.
The Basics of Medical Injection Molding:
At its core, medical injection molding involves the creation of intricate and precise components by injecting molten material into a mold cavity. The process typically begins with the selection of a thermoplastic resin suitable for the specific application and requirements of the medical device.
Key Steps in the Medical Injection Molding Process:
- Design and Mold Creation: The process starts with the design of the mold. Which is crucial for achieving the desired shape and functionality of the final product. Computer-aided design (CAD) software is often utilized to create precise blueprints of the mold.
- Material Preparation: Once the mold design is finalized, the selected thermoplastic material is prepared for the injection molding process. This involves melting the resin to a precise temperature to ensure proper flow and filling of the mold cavities.
- Injection Molding: The molten material is then injected into the mold under high pressure using specialized equipment. The pressure ensures that the material fills the mold completely and that any intricate details are accurately replicated.
- Cooling and Solidification: After the mold cavity is filled. The molten material is allowed to cool and solidify within the mold. The cooling process is carefully controlled to prevent warping or defects in the final product.
- Ejection: Once the material has cooled and solidified, the mold opens, and the newly formed component is ejected from the mold cavity. This step requires precision to avoid damaging the component or the mold.
- Post-Processing: Depending on the specific requirements of the medical device, additional post-processing steps such as trimming. Surface finishing, or assembly may be necessary to achieve the final product.
Benefits of Medical Injection Molding:
- Precision and Consistency: Medical injection molding allows for the production of highly precise and consistent components, ensuring uniformity in medical devices.
- Cost-Efficiency: Mass production capabilities of injection molding result in lower per-unit costs, making it a cost-effective manufacturing solution for medical devices.
- Material Versatility: A wide range of thermoplastic materials can be used in medical injection molding. Offering flexibility in design and functionality to meet diverse medical needs.
- Regulatory Compliance: Medical injection molding processes are subject to stringent quality control measures and regulatory standards to ensure the safety and efficacy of medical devices.
Advanced Techniques and Innovations in Medical Injection Molding
In recent years, advancements in technology and materials have further enhanced the capabilities and efficiency of medical injection molding. These innovations have revolutionized the production of medical devices, allowing for greater customization, improved performance, and enhanced patient outcomes.
1. Micro-Molding:
Micro-molding is a specialized form of injection molding that enables the production of extremely small and intricate components with micron-level precision. This technique is particularly valuable in the manufacturing of minimally invasive medical devices such as catheters, implantable devices, and microfluidic systems. Micro-molding allows for the creation of complex geometries and precise features that are essential for the functionality of these devices.
2. Multi-Shot Molding
Multi-shot molding, also known as two-shot or multi-material molding, enables the production of components with multiple materials or colors in a single molding cycle. This technique is advantageous for medical devices that require different materials or properties in specific areas, such as soft-touch grips, over-molded seals, or biocompatible coatings. Multi-shot molding reduces assembly time, enhances product performance, and improves the overall aesthetics of medical devices.
3. Cleanroom Molding
Molding is a specialized manufacturing environment designed to minimize contamination and ensure the cleanliness and sterility of medical devices. Cleanroom facilities adhere to strict cleanliness standards, including controlled air quality, temperature, and humidity, to prevent the introduction of contaminants during the injection molding process. Cleanroom molding is essential for producing medical devices that require a sterile or aseptic environment. Such as surgical instruments, implantable devices, and diagnostic equipment.
4. Insert Molding:
Insert molding involves the over-molding of metal or plastic inserts, such as threaded fasteners, electronic components, or sensors, which are then combined with thermoplastic material to create a single integrated component. This process improves product durability, reduces assembly costs, and enhances the overall performance of medical devices. Furthermore, insert molding is commonly used in the production of disposable medical instruments, patient monitoring devices, and wearable sensors.
5. Advanced Materials:
The development of specialized medical-grade materials has expanded the possibilities for medical injection molding. Additionally, biocompatible polymers, such as thermoplastic elastomers (TPEs), bioabsorbable polymers, and antimicrobial additives, offer enhanced functionality and safety for medical devices. Moreover, these materials exhibit properties such as flexibility, durability, and resistance to chemical sterilization methods, making them ideal for a wide range of medical applications.
Conclusion
Medical injection molding continues to evolve with advancements in technology, materials, and manufacturing techniques. From micro-molding for miniaturized devices to cleanroom molding for sterile environments. These innovations enable the production of high-quality, reliable medical devices that improve patient care and outcomes. By leveraging the latest advancements in medical injection molding. Manufacturers can continue to push the boundaries of innovation and address the evolving needs of the healthcare industry.
Also Read: From Zero to Certification Mental Health Coaching