Waterproof Connectors 101: A Comprehensive Guide to Types and Applications
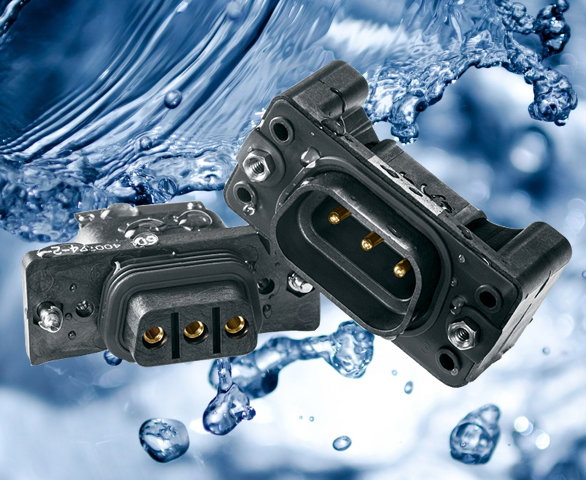
Waterproof connectors are an essential component in many industries where electrical connections are exposed to harsh environmental conditions. These connectors are designed to provide a reliable and secure connection, even in wet or dusty environments. In this comprehensive guide, we will explore the different types of waterproof connectors, their applications, and the factors to consider when choosing the right connector for your needs.
Contents
- Importance of Waterproof Connectors in Various Industries
- Key Features and Benefits of Waterproof Connectors
- Types of Waterproof Connectors
- Applications of Waterproof Connectors in Different Industries
- Factors to Consider When Choosing Waterproof Connectors
- Installation and Maintenance of Waterproof Connectors
- How to Troubleshoot Common Issues with Waterproof Connectors
- Conclusion and Final Thoughts
Importance of Waterproof Connectors in Various Industries
Waterproof connectors play a crucial role in a wide range of industries, including marine, automotive, telecommunications, and outdoor lighting. In the marine industry, for example, waterproof connectors are used to connect navigation equipment, underwater lights, and communication systems. These connectors ensure that the electrical connections remain intact and functional, even when exposed to saltwater and extreme weather conditions.
Similarly, in the automotive industry, waterproof connectors are used to connect various electrical components such as sensors, lights, and control modules. These connectors are designed to withstand vibrations, temperature variations, and exposure to chemicals. Without waterproof connectors, the electrical connections in these industries would be susceptible to corrosion, moisture ingress, and ultimately, failure.
Key Features and Benefits of Waterproof Connectors
Waterproof connectors come with several key features and benefits that make them an ideal choice for demanding environments. One of the primary features of waterproof connectors is their ability to provide a tight seal that prevents water, dust, and other contaminants from entering the connection. This ensures the reliability and longevity of the electrical system.
Furthermore, waterproof connectors are designed to withstand extreme temperatures, ranging from freezing cold to scorching heat. They are also resistant to chemicals, UV radiation, and mechanical stress. These features make them suitable for outdoor applications, where the connectors are exposed to various environmental factors.
Another advantage of waterproof connectors is their ease of installation. Most connectors are plug-and-play, allowing for quick and hassle-free installation. Additionally, many waterproof connectors are designed with a locking mechanism that ensures a secure connection, even in high-vibration environments.
Types of Waterproof Connectors
RJ45 Waterproof Connector
The RJ45 waterproof connector is a popular type of waterproof connector commonly used in networking applications. It is designed to provide a waterproof and dustproof connection for Ethernet cables. These connectors are commonly used in outdoor networking installations, such as in industrial settings, outdoor surveillance systems, and outdoor Wi-Fi networks.
RJ45 waterproof connectors typically have an IP (Ingress Protection) rating, which indicates their level of protection against water and dust. The higher the IP rating, the more protected the connector is. These connectors are available in various configurations, including straight, angled, and panel-mount, to suit different installation requirements.
Plastic Circular Connectors
Plastic circular connectors are another type of waterproof connector widely used in various industries. These connectors are made of durable plastic materials, which provide excellent resistance against moisture, chemicals, and UV radiation. Plastic circular connectors are commonly used in outdoor lighting systems, solar power installations, and agricultural equipment.
One of the key advantages of plastic circular connectors is their versatility. They are available in multiple sizes, pin configurations, and IP ratings, allowing for flexibility in different applications. These connectors are also easy to assemble and disassemble, making maintenance and repairs hassle-free.
Cable Joining Kits
Cable joining kits are a convenient solution for creating waterproof connections in cables. These kits typically include heat shrink tubing, solder, and adhesive-lined heat shrink sleeves. Cable joining kits are commonly used in underground cable installations, outdoor electrical connections, and marine applications.
To use a cable joining kit, the damaged or cut cables are first stripped of their insulation. The heat shrink tubing is then slid over the stripped portion of the cable, and the solder is applied to the exposed wires. Finally, the adhesive-lined heat shrink sleeve is placed over the soldered area and heated to create a waterproof seal.
Applications of Waterproof Connectors in Different Industries
Waterproof connectors find applications in a wide range of industries due to their ability to provide reliable and secure connections in challenging environments. In the marine industry, waterproof connectors are used in navigation systems, underwater lights, and communication equipment. In the automotive industry, these connectors are used in sensors, lights, and control modules.
In the telecommunications industry, waterproof connectors are used in outdoor networking installations, such as Wi-Fi networks, surveillance systems, and remote monitoring equipment. In the outdoor lighting industry, waterproof connectors are used in landscape lighting systems, streetlights, and architectural lighting.
Moreover, waterproof connectors are also used in the renewable energy sector, including solar power installations and wind turbines. These connectors ensure the efficient and reliable transmission of electrical power in these environmentally demanding applications.
Factors to Consider When Choosing Waterproof Connectors
When choosing waterproof connectors, several factors should be considered to ensure the right fit for the intended application. One of the essential factors is the IP rating of the connector. The IP rating determines the level of protection against water and dust. It is crucial to choose a connector with a suitable IP rating that matches the environmental conditions in which it will be used.
Another factor to consider is the connector’s material and construction. Different materials offer varying levels of resistance to moisture, chemicals, and temperature extremes. It is important to select a connector made of materials that can withstand the specific environmental conditions.
Additionally, the connector’s size, pin configuration, and mounting options should be considered to ensure compatibility with existing equipment and installation requirements. It is also important to evaluate the connector’s ease of installation and maintenance, as this can affect the overall efficiency and cost-effectiveness of the electrical system.
Installation and Maintenance of Waterproof Connectors
Proper installation and maintenance of waterproof connectors are crucial for maintaining their performance and reliability. During installation, it is essential to ensure that the connectors are securely mated and that any sealing mechanisms, such as rubber gaskets or o-rings, are properly aligned and undamaged.
Regular inspection and cleaning of the connectors are also important to remove any dirt, dust, or moisture that may have accumulated over time. If any damage or wear is detected, the connectors should be replaced promptly to prevent potential failures.
How to Troubleshoot Common Issues with Waterproof Connectors
Despite their robust design, waterproof connectors may occasionally encounter issues that affect their performance. Some common problems include poor conductivity, water ingress, and connector degradation. To troubleshoot these issues, it is important to first inspect the connectors for any visible damage or loose connections.
If poor conductivity is detected, cleaning the connectors with a suitable contact cleaner and ensuring proper alignment during reconnection can often resolve the issue. In the case of water ingress, inspecting the sealing mechanisms and replacing damaged seals can help restore the waterproof integrity of the connectors.
If connector degradation is observed, such as cracking or corrosion, it is advisable to replace the connectors to prevent any further deterioration of the electrical system. Regular inspections and preventive maintenance can help identify and address these issues before they cause significant disruptions.
Conclusion and Final Thoughts
Waterproof connectors are vital components in various industries where reliable electrical connections are required in challenging environments. Their ability to provide a secure and waterproof connection ensures the integrity and longevity of electrical systems in marine, automotive, telecommunications, and outdoor lighting applications.
When choosing waterproof connectors, it is important to consider factors such as IP rating, material, size, and ease of installation. Regular maintenance and troubleshooting are essential to ensure optimal performance and prevent potential failures.
By understanding the different types of waterproof connectors, their applications, and the factors to consider when selecting them, you can make informed decisions that meet your specific needs. Investing in high-quality waterproof connectors will ultimately result in reliable and durable electrical connections that withstand the harshest conditions.
For more information on waterproof connectors and to explore our range of high-quality products, please visit our website or contact our expert team today.