Understanding the Vital Components of Medical Plastic Injection Molding
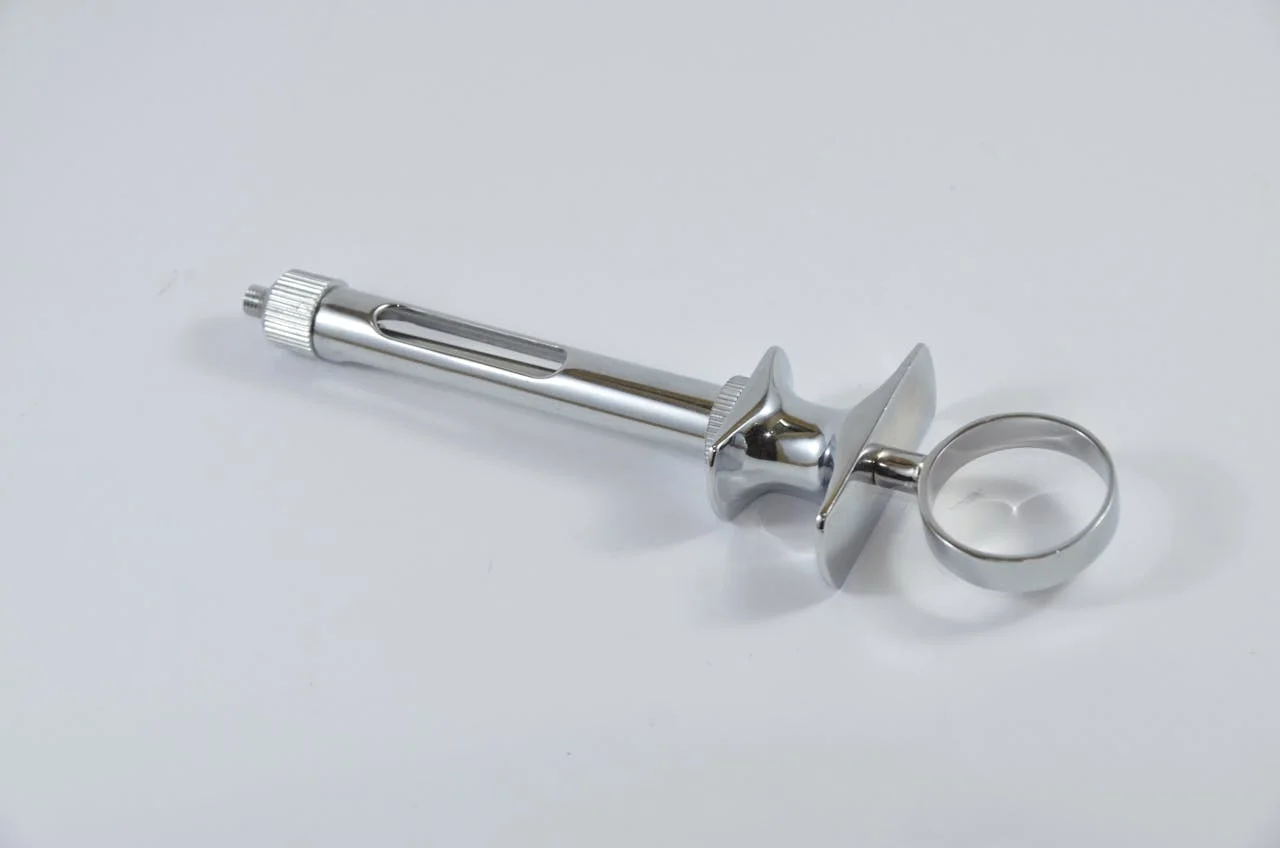
Medical plastic injection molding stands as a cornerstone in the manufacturing of various medical devices and equipment. This process plays a critical role in producing intricate and precise components vital for healthcare applications. To comprehend its significance fully, it’s imperative to delve into the key components that make medical plastic injection molding indispensable in the healthcare industry.
Contents [show]
Precision and Accuracy
In the realm of medical devices, precision and accuracy are non-negotiable. Medical plastic injection molding ensures the production of components with unparalleled precision. Adhering to strict tolerances essential for the functionality and safety of medical devices. Whether it’s intricate geometries or micron-level details, the process guarantees consistency and accuracy, minimizing the margin for error.
Material Selection and Biocompatibility
The materials used in medical plastic injection molding must meet stringent standards for biocompatibility and chemical resistance. From thermoplastics like polycarbonate to medical-grade elastomers such as silicone, each material undergoes rigorous testing to ensure compatibility with biological systems and resistance to sterilization methods. This meticulous selection process ensures that the final products are safe for use within the human body without triggering adverse reactions.
Cleanroom Manufacturing
Maintaining a sterile environment is paramount in medical device manufacturing. Medical plastic injection molding often takes place in cleanroom facilities equipped with advanced filtration systems to prevent contamination. Strict adherence to cleanroom protocols mitigates the risk of bacterial or particulate contamination, safeguarding the integrity of the final products and ensuring compliance with regulatory standards.
Quality Control and Validation
The stringent regulatory landscape governing the healthcare industry necessitates robust quality control measures throughout the manufacturing process. From initial design validation to in-process inspections and final product testing, medical plastic injection molding undergoes rigorous scrutiny at every stage. Advanced metrology tools, including coordinate measuring machines (CMMs) and optical inspection systems, are employed to verify dimensional accuracy and structural integrity, guaranteeing that each component meets or exceeds regulatory requirements.
Cost Efficiency and Scalability
Despite the intricate nature of medical plastic injection molding, manufacturers strive to maintain cost efficiency without compromising on quality. Advanced mold design techniques, such as multi-cavity molds and hot runner systems, optimize production cycles and minimize material wastage. Resulting in cost-effective manufacturing solutions. Furthermore, the scalability of injection molding allows for high-volume production, ensuring timely delivery of medical devices to meet growing healthcare demands.
Molding: Pioneering Innovation for Healthcare
As technology evolves and healthcare demands become increasingly complex, the field of medical plastic injection molding continues to push boundaries and pioneer innovations. Here are some notable advancements shaping the landscape of medical device manufacturing:
1. Micro-Molding Technology:
The emergence of micro-molding technology has revolutionized the production of miniature medical components with unprecedented precision. Utilizing specialized equipment and advanced tooling techniques, micro-molding enables the fabrication of intricate features and ultra-small geometries, opening new possibilities for minimally invasive medical devices and implantable sensors.
2. Biodegradable and Bioresorbable Polymers:
With a growing emphasis on sustainability and patient comfort, manufacturers are exploring biodegradable and bioresorbable polymers for medical device applications. Medical plastic injection molding facilitates the production of implantable devices and drug delivery systems using materials that degrade over time within the body, eliminating the need for surgical removal and reducing environmental impact.
3. Overmolding and Insert Molding:
Overmolding and insert molding techniques allow for the integration of multiple materials or components into a single device. Enhancing functionality and design flexibility. By encapsulating electronics, incorporating soft-touch grips, or bonding dissimilar materials, medical plastic injection molding enables the creation of innovative medical devices with seamless integration of disparate elements.
4. Additive Manufacturing Integration:
The integration of additive manufacturing processes. Such as 3D printing, with traditional injection molding techniques has accelerated prototyping and streamlined production workflows in medical device manufacturing. By leveraging the design freedom and rapid iteration capabilities of additive manufacturing,. Manufacturers can expedite the development of complex tooling and iterate on product designs more efficiently, ultimately reducing time-to-market for medical devices.
5. Real-time Monitoring and Quality Assurance:
Incorporating real-time monitoring and quality assurance systems into medical plastic injection molding processes enhances process visibility and product traceability. Advanced sensors, data analytics, and machine learning algorithms enable manufacturers to monitor key process parameters in real-time. Detect anomalies, and preemptively address issues, ensuring consistent product quality and compliance with regulatory standards.
Conclusion:
The convergence of cutting-edge technologies and continuous process improvement is driving unprecedented innovation in medical plastic injection molding. From micro-molding advancements to the integration of additive manufacturing and real-time monitoring systems, these advancements are reshaping the landscape of healthcare manufacturing. Enabling the development of safer, more effective medical devices to address the evolving needs of patients and healthcare providers alike. As the industry continues to evolve, medical plastic injection molding remains a cornerstone of innovation. Driving progress and pushing the boundaries of what’s possible in healthcare.
Also Read: How Can Consent Management Platforms Be Beneficial for Businesses Today?