Gravity Die Casting Process in 5 Steps
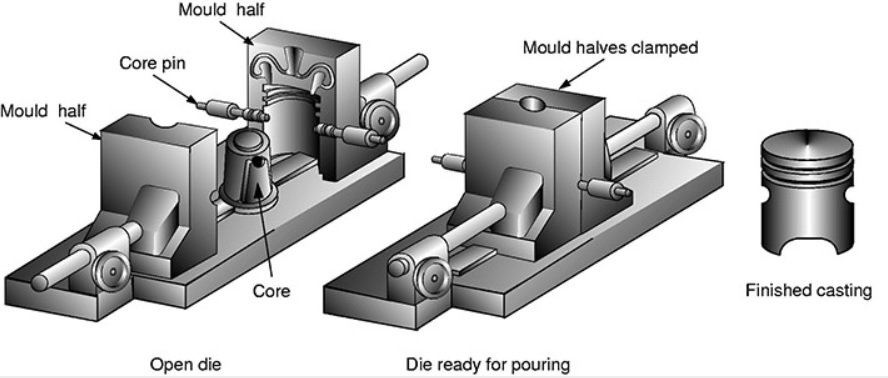
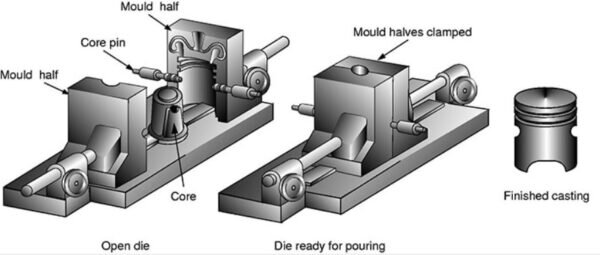
Welcome to the world of precision engineering! Today, we are going to take you on an exhilarating journey through the gravity die casting process steps. Buckle up and prepare to be blown away by the magic that happens when molten metal meets gravity and craftsmanship. Whether you’re a seasoned engineer or simply someone fascinated by how things are made, this blog post will provide you with a captivating insight into the five essential steps involved in creating exceptional castings. So, grab your safety goggles, and let’s dive into the extraordinary world of gravity die casting!
Contents [show]
What is Gravity Die Casting?
Gravity die casting, also known as permanent mold casting, is a metal casting process that involves pouring molten metal into a reusable mold under the force of gravity. Unlike other methods like sand casting or investment casting, gravity die casting process steps utilizes a metallic mold that can be used multiple times, making it highly cost-effective and efficient.
- The process starts with the design and preparation of the mold. The mold is typically made from steel or cast iron and consists of two halves: the cope and drag. These halves are precisely machined to create cavities in which the molten metal will solidify.
- Once the mold is ready, it’s time for step two: heating and pouring the molten metal. The chosen alloy is melted in a furnace at high temperatures until it reaches its liquid form. Then, using either ladles or automated systems, the molten metal is poured into the prepared molds.
- Next comes step three: gravity force and filling of the mold cavity. As soon as the molten metal enters the mold cavity through gates and runners, gravity takes over to ensure complete filling without any external pressure required.
- Step four focuses on solidification and cooling of the metal within the mold cavity. This stage requires precise timing to allow sufficient cooling for proper solidification while avoiding any shrinkage defects.
- We reach step five: removal and finishing of the casted part.
The 5 Steps of Gravity Die Casting
The gravity die casting process steps involves five imprtant steps:
Step 1: Design and Preparation of the Mold
- Begin with designing a detailed blueprint, outlining specifications and features.
- Select suitable materials for mold construction, ensuring durability.
- Utilize machining or CNC milling to create precise mold cavities.
- Finish the mold surface meticulously for smooth molten metal flow.
- Add necessary inserts like cores or pins for complex shapes.
Step 2: Heating and Pouring of Molten Metal
- Heat the chosen alloy in a furnace to its melting point.
- Carefully pour the molten metal into molds, utilizing gravity for even distribution.
- Ensure uniform temperature and pouring speed for quality castings.
Step 3: Gravity Force and Filling of the Mold Cavity
- Employ gravity to fill mold cavities as molten metal flows naturally.
- Control temperature, viscosity, and pouring speed for defect-free results.
Step 4: Solidification and Cooling of the Metal
- Allow the molten metal to cool and solidify to achieve the desired properties.
- Ensure proper cooling techniques to avoid defects.
- Cooling time varies depending on the part size and geometry.
Step 5: Removal and Finishing of the Casted Part
- Carefully separate mold halves to reveal the casted part.
- Remove excess material or flash using techniques like trimming or grinding.
- Apply finishing touches such as polishing, buffing, drilling, or tapping to meet quality standards and specifications.
These steps collectively result in high-quality casted parts, suitable for various applications across industries. The gravity die casting process steps combines precision and craftsmanship to create complex geometries with excellent mechanical properties.
Advantages and Applications of Gravity Die Casting
Gravity die casting offers several advantages that make it a popular choice for many manufacturing applications.
- One key advantage is the high dimensional accuracy achieved through this process. The use of permanent molds ensures consistent results, producing parts with precise dimensions and minimal variations.
- Another benefit of gravity die casting is its ability to produce complex shapes with intricate details. The molten metal flows evenly into the mold cavity under gravity force, allowing for the creation of intricate features such as thin walls, sharp corners, and fine surface finishes.
- Gravity die casting yields castings with excellent mechanical properties. The controlled cooling process during solidification enhances the material’s strength and durability, resulting in parts that can withstand high stress and perform reliably in demanding environments.
- Gravity die casting offers cost-effective production capabilities. With shorter cycle times compared to other casting methods like sand casting or investment casting, manufacturers can achieve higher productivity levels while maintaining consistent quality standards.
- The versatility of gravity die casting also makes it suitable for various industries and applications. It is commonly used in automotive manufacturing for engine components such as cylinder heads and intake manifolds due to its superior strength-to-weight ratio. Additionally, aerospace companies rely on this process to create precision parts like turbine blades that require tight tolerances.
Gravity die casting presents numerous advantages for manufacturers seeking high-quality castings with complex geometries. Its accurate dimensional control, ability to produce detailed shapes, excellent mechanical properties, cost-effectiveness, and wide range of applications make it a preferred choice across different industries. Whether you’re looking to manufacture automotive components or intricate aerospace parts, gravity die casting can deliver the results you need efficiently and effectively
Common Mistakes to Avoid in Gravity Die
In gravity die casting, several common mistakes can lead to defects in casted parts and impact the overall quality of the process. To ensure a successful casting process and high-quality parts, it’s important to avoid these pitfalls:
- Improper Mold Design: Neglecting factors like shrinkage, draft angles, and gating system placement can result in incomplete fillings or metal flow issues.
- Inadequate Heating and Pouring: Ensuring that the molten metal reaches the correct temperature and using proper pouring techniques is essential to avoid poor fillings and turbulence.
- Neglecting Gravity Force: Failing to account for gravity force in the gating system and venting channels can lead to trapped gases within the part, causing porosity defects.
- Overlooking Solidification and Cooling: Rushing through solidification and cooling can result in insufficient solidification and uneven cooling rates, leading to internal stress and dimensional instability.
- Neglecting Post-Casting Processes: Inadequate removal of excess material and surface treatments can result in rough surfaces or compromised dimensions in the final product.
By being aware of these common mistakes and taking proactive measures during each step of the gravity die casting process, you can increase your chances of achieving high-quality casted parts efficiently. Remember to pay attention during mold design, heat metals correctly, consider gravity forces, allow sufficient solidification time, and don’t forget post-casting processes.
Also Read: Understanding Factors That Impact Storage Unit Prices in San Francisco
Conclusion
The final casted part, the removal, and finishing of the casted part, is crucial for ensuring that the product meets quality standards. Careful handling and precise techniques, such as trimming, grinding, and polishing, result in a high-quality end product ready for various industrial applications. Gravity die casting offers numerous advantages, including high dimensional accuracy, the ability to create complex shapes, excellent mechanical properties, cost-effective production, and versatility across industries.
To achieve successful gravity die casting, it’s important to avoid common mistakes related to mold design, heating and pouring, gravity force, solidification, and post-casting processes. Understanding and executing the gravity die casting process steps with precision can lead to the creation of intricate and high-quality metal components, making it a valuable method in the world of manufacturing.