Elevating Food Excellence: Unveiling the Crucial Role of Vibratory Screeners in Ensuring Food Quality
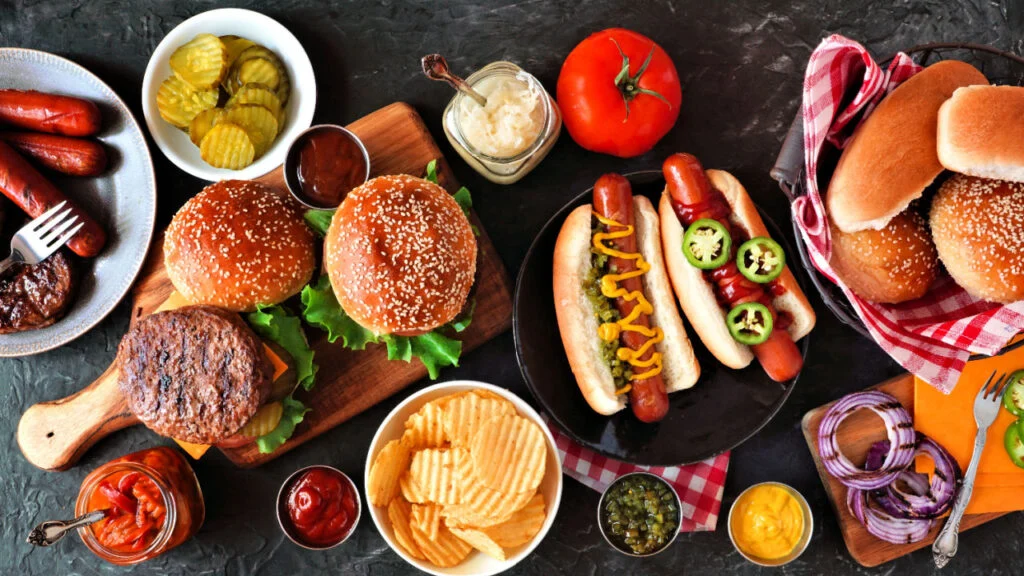
In the intricate domain of food production, ensuring the highest level of quality is not merely a goal – it’s an absolute necessity. As the food industry continually seeks innovative ways to improve processes and elevate standards, the role of the vibratory screener emerges as a critical factor in maintaining and enhancing food quality across the board.
The vibratory screener, an unassuming yet indispensable piece of equipment, plays a multifaceted role in upholding food quality. At its core, a vibratory screener is a machine designed to segregate particles based on size. It achieves this by employing vibrations to facilitate the movement of particles through a screen or mesh. This seemingly simple process, however, yields a myriad of benefits that significantly impact food quality.
Foremost among its contributions is the assurance of a pristine product. Raw materials, despite rigorous sourcing, can contain unwanted elements such as foreign particles, contaminants, or impurities. Vibratory screeners act as a stringent gatekeeper, meticulously sieving out these undesirable components to deliver a product of unparalleled purity. By doing so, they not only enhance the sensory and visual appeal of the final product but also underscore the commitment of food manufacturers to uncompromising quality.
Beyond enhancing aesthetics, vibratory screeners play a pivotal role in guaranteeing food safety. In an era where consumer health and well-being are paramount concerns, mitigating the risks of foodborne illnesses is non-negotiable. The microorganisms or pathogens that can infiltrate raw materials pose a potential threat to consumers’ health. Vibratory screeners equipped with fine mesh screens act as an effective barrier, preventing the passage of even the tiniest contaminants. By acting as a first line of defense, these screeners bolster food safety measures and prevent the potential backlash of recalls or compromised consumer trust.
Consistency is another hallmark of food quality, particularly concerning products with specific texture requirements or uniformity expectations. A vibratory screener comes to the fore by ensuring a consistent particle size distribution. This consistency translates to uniform texture, improved flavor release, and even cooking or processing times. In industries where particle size directly influences product quality, such as baking or spice production, the screener becomes an indispensable tool for maintaining the desired characteristics of the end product.
Operational efficiency is a paramount consideration for any food manufacturer, and vibratory screeners excel in optimizing processes. Their ability to swiftly sift through large volumes of material significantly reduces processing time, leading to increased productivity without compromising on quality. This becomes especially pertinent when scaling up production to meet market demands. By streamlining the screening process, manufacturers can strike a delicate balance between quantity and quality.
One of the noteworthy aspects of vibratory screeners is their adaptability to a diverse range of food products. Whether dealing with dry powders, viscous liquids, or delicate produce, these screeners can be tailored to suit various processing needs. This versatility positions them as a cornerstone in various segments of the food industry, from dairy to beverages, and beyond.
In closing, the vibratory screener emerges as a silent sentinel, working tirelessly to uphold the principles of food quality in a dynamic and evolving industry. Its role in sifting out impurities, ensuring uniformity, and expediting production processes contributes to an elevated standard of the final product. As technology advances, we can anticipate even more sophisticated iterations of vibratory screeners that will continue to redefine and elevate the landscape of food quality assurance.