Choosing the Right Metal Cutters for Your Fabrication Needs
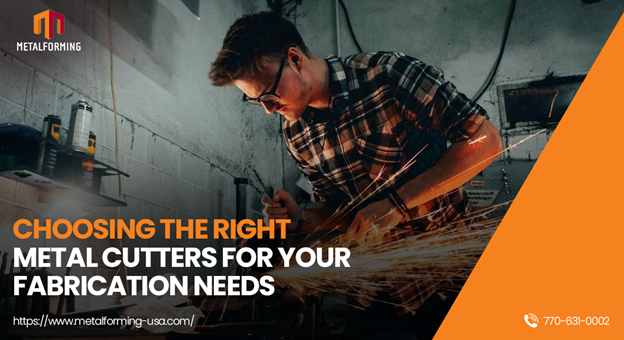
Selecting the appropriate metal cutters is pivotal for achieving precision, efficiency, and safety in the metal fabrication industry. Metal cutters play an essential role in shaping and customizing metal components to fit specific design requirements, making them indispensable in workshops, manufacturing plants, and construction sites. This article delves into the various types of metal cutters and their applications, followed by essential tips for their maintenance, ensuring their longevity and optimal performance.
Contents
Different Types of Metal Cutters and Their Uses
Metal fabrication demands a diverse set of tools to cut through metals of varying thicknesses and hardness. Understanding the capabilities and applications of these cutting tools for metalwork is crucial for selecting the best metal cutters for your project needs.
Handheld Metal Cutters
These are versatile and portable tools ideal for quick and straightforward cutting tasks. Handheld metal cutters include tin snips, hacksaws, and bolt cutters, each designed for specific types of cuts and metal thicknesses. They are perfect for on-site adjustments and minor projects where precision and fine control are required.
Saws
Saws are among the most commonly used cutting tools in metal fabrication. They range from manual hacksaws to sophisticated power saws like band saws, circular saws, and reciprocating saws. Each saw type has its unique blade design and cutting technique, making them suitable for various metal cutting tasks, from straight cuts to complex shapes.
Drills
While primarily used for creating holes, drills equipped with hole saw attachments can effectively cut through metal. Drill presses and magnetic drills offer more stability and precision, making them ideal for repetitive tasks requiring high accuracy.
Lathes
Lathes are not traditional cutters but play a critical role in shaping metal by rotating it against a cutting tool. They are indispensable for creating cylindrical parts with precise dimensions, such as bolts and threaded components.
Mills
Milling machines use rotary cutters to remove metal and shape the workpiece. With capabilities for precision metal cutting, mills are essential for detailed work on metal parts, including slots, grooves, and other complex shapes.
Plasma Cutters
For cutting thick metal sheets and plates, plasma cutters are the go-to equipment. They use a high-velocity jet of ionized gas to melt and eject material from the cut, offering speed and precision even in heavy-duty metal cutting tasks.
Water Jets
Water jet cutters use high-pressure water, sometimes mixed with abrasive materials, to cut metal. They are renowned for their precision and the ability to cut without inducing heat, making them ideal for materials sensitive to thermal distortion.
Tips for Maintaining Your Metal Cutters
Proper maintenance of your metal cutters is crucial to ensure they remain in top condition, providing precise cuts and extending their lifespan. Here are essential tips for keeping your cutting tools in optimal shape:
Routine Inspections
Regularly inspect your metal cutters for signs of wear, damage, or alignment issues. Even minor damage can lead to significant problems if left unaddressed. Routine inspections help identify issues early, allowing for timely repairs or adjustments. This proactive approach can prevent costly downtime and ensure that your metal cutters are always ready for the job at hand.
Regular Cleaning
After each use, clean your metal cutters to remove any metal filings, dust, or residues. This prevents the build-up of materials that can dull the cutting edges over time. For handheld metal cutters, wiping them with a clean cloth and applying a light oil coating can prevent rust and corrosion.
Lubrication
Keeping your cutting tools well-lubricated is vital, especially for mechanical and power cutters. Lubrication reduces friction during cutting, which can otherwise lead to excessive wear and tear. Follow the manufacturer’s recommendations for the type and frequency of lubrication.
Sharpening
Dull cutting edges not only make your job harder but can also compromise the quality of your cuts. Regularly inspect the blades or cutting edges of your metal cutters and have them sharpened or replaced as necessary. This ensures clean, efficient cuts and reduces the effort required during operation.
Proper Storage
Store your metal cutters in a dry, clean environment to prevent rust and damage. Handheld metal cutters should be kept in their original cases or hung on a tool rack to protect their cutting edges. For industrial cutting equipment, cover them to protect against dust and moisture.
Safety Checks
Before each use, perform a safety check on your metal cutters to ensure all components are secure and in good working order. This includes checking for loose parts, damaged cables, and ensuring that safety guards are in place. Adhering to safety tips for metal cutting not only protects the tool but also the user.
Training
Ensure that anyone using the metal cutters is properly trained. Understanding the correct use and handling of these tools is essential for their maintenance and the safety of the operator. Comprehensive knowledge about cutting techniques for metal also maximizes the efficiency and effectiveness of the cutting process.
Final Thoughts
Choosing the right metal cutters for your fabrication needs requires an understanding of the different types available and their specific uses. Once you have selected the appropriate cutting tools, maintaining them through regular cleaning, lubrication, sharpening, and proper storage will ensure they remain reliable, durable metal cutting tools for years to come. By following these guidelines, you can achieve precision in your metalwork projects while ensuring the safety and longevity of your equipment.
Frequently Asked Questions
What types of metal cutters are available?
Various types of metal cutters include handheld snips, saws (band, circular, reciprocating), drills with cutting attachments, lathes, mills, plasma cutters, and water jets. Each is designed for specific tasks, such as precise cuts, heavy-duty slicing, or detailed shaping of metal components.
How do I choose the right metal cutter for my project?
To choose the right metal cutter, consider the material thickness, the precision required, and the type of cut needed. For intricate shapes, opt for mills or plasma cutters. For straight, long cuts, saws are ideal. Evaluate your project’s specific needs and the cutter’s capabilities to ensure compatibility.