Large injection molding machine for High-Pressure Applications
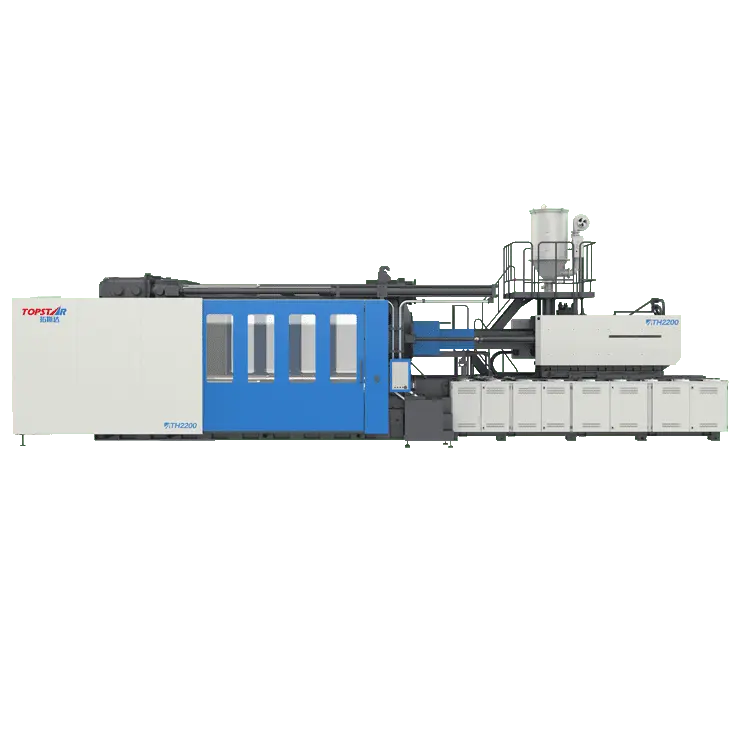
In the injection molding manufacturing industry, increased demand for complex and high-strength parts has driven the need for machines that can withstand intense pressure and function adequately. Therefore, the role of large injection molding machines in high-pressure applications is crucial. This article explores the capabilities of large injection molding machines tailored for high-pressure applications.
Contents [show]
Design features of large injection molding machines
Tailored for high-pressure applications, large injection molding machines’ sturdy frames and reinforced components can withstand harsh, high pressures while maintaining optimal performance. Their advanced hydraulic systems provide the force and control to form complex high-strength parts. These machines often employ innovative cooling systems to manage the thermal stresses associated with high-pressure molding. An efficient cooling system is critical to maintaining consistent temperature conditions during molding. Large injection molding machines use advanced cooling technology to dissipate heat and prevent heat-related problems effectively, such as the efficient heat dissipation mechanism, which ensures consistent performance even under prolonged high-pressure conditions.
Control system of large injection molding machine
Large injection molding macghines use state-of-the-art control systems to coordinate all aspects of the molding process. From adjusting injection speed to ensuring consistent pressure, these systems help produce perfect parts. Large injection molding machines often use advanced servo motor technology. These motors precisely control the movement of components, allowing for precise positioning and injection processes. The control system utilizes a closed-loop feedback mechanism in which sensors continuously monitor vital parameters such as pressure, temperature, and position. This real-time feedback allows the system to make immediate adjustments for optimal accuracy. Their advanced sensors and feedback mechanisms provide real-time data, allowing operators to fine-tune parameters and achieve desired results. The synergy between robust mechanical design and sophisticated control systems sets these machines apart, making them indispensable for high-precision applications.
The driving force behind large injection molding machine
The main driver is the ability of large injection molding machines to produce large quantities of components efficiently. This scalability ensures cost-effective manufacturing, especially for industries that require large amounts of identical or customized parts. They can also accommodate complex part geometries, providing unparalleled design flexibility. This capability is critical for industries that require diverse and complex components to achieve product functionality and aesthetics. Advances in mold design and technology have enhanced the capabilities of large-scale injection molding. Innovative tooling solutions help speed up production cycles, reduce lead times, and improve efficiency.
Large injection molding machine of high-performance polymers
High-pressure applications often require high-performance polymers to meet specific mechanical and thermal requirements. Large injection molding machines excel at processing various materials, including reinforced plastics and high-performance polymers. Thermoplastic composites can improve mechanical properties which combining polymers with reinforcing fibers or fillers. This results in improved strength-to-weight ratio, impact resistance, and dimensional stability of the component. Large injection molding supports chemically resistant polymers such as PTFE, PVDF, or PPS. These materials are critical for high-pressure applications exposed to corrosive environments, such as chemical processing equipment or automotive components.
Overcome challenges
Overcoming the challenges of large-scale injection molding in high-pressure die casting involves addressing various scale, precision, and materials-related complexities. Managing the complex flow dynamics of molten material in large molds is a challenge. Use advanced simulation tools to optimize material flow and prevent problems such as air entrapment, incomplete filling, or uneven distribution. Large molds generate large amounts of heat during the injection process, and using advanced cooling systems and materials with enhanced thermal conductivity is critical to preventing overheating and ensuring consistent part quality. Especially in mass production, complex control mechanisms are required. Implementing advanced mold design strategies, in-mold sensors, and automatic adjustments can improve the accuracy of multi-cavity molding.
In general
The rugged design, sophisticated control systems, and versatility of material selection of large injection molding machines make them critical tools for industries that require complex and high-strength parts. Whether in automotive, aerospace, or other high-performance fields, the capabilities of large injection molding machines provide precise and reliable assistance.
Also Read: Key Factors to Consider When Buying an Alkaline Water Machine