FAQ: Advanced Understanding of Additive Manufacturing
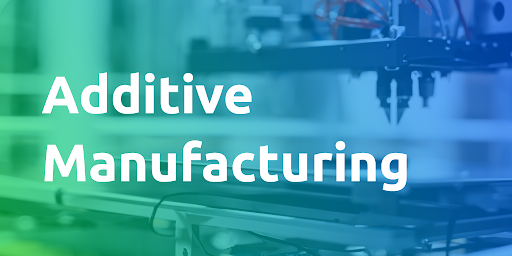
Contents [show]
General
1. How has Additive Manufacturing (AM) evolved from prototyping to full-scale production?
AM has transitioned from a rapid prototyping tool to a full-scale production method by improving material properties, process reliability, and cost efficiency. Advances in Design for Additive Manufacturing (DfAM) allow for industrial-grade components in aerospace, medical, automotive, and consumer industries.
2. What are the key factors in achieving optimal performance in AM?
Performance in AM depends on material selection, process optimization, and post-processing. Factors such as mechanical properties, thermal stability, and cost must be considered when choosing materials and design strategies.
3. Why is Design for Additive Manufacturing (DfAM) important?
DfAM optimizes part geometry, minimizes material waste, and reduces post-processing requirements. It ensures manufacturability while maintaining strength, weight efficiency, and cost-effectiveness.
4. What are the main topics covered in this document regarding AM?
The document covers material selection, process guidelines, cost considerations, production optimization, and industry applications.
Material Selection
5. What are the primary material categories used in AM?
The three main categories are:
- Polymers (e.g., PLA, ABS, Nylon)
- Metals (e.g., Titanium, Stainless Steel, Inconel)
- Composites (e.g., Carbon Fiber-Reinforced Polymers)
6. How does material selection impact mechanical performance and post-processing requirements?
Material properties dictate durability, thermal resistance, and strength. Some materials require additional processing, such as heat treatment for metals or surface finishing for polymers.
Polymers in Additive Manufacturing
7. What are the advantages and disadvantages of using polymers in AM?
- Advantages: Affordable, lightweight, and versatile
- Disadvantages: Limited mechanical strength compared to metals and composites
8. How do Fused Deposition Modeling (FDM), Selective Laser Sintering (SLS), and Stereolithography (SLA) differ in polymer AM?
- FDM: Low-cost, good for prototypes but lower surface quality
- SLS: Powder-based, high strength, no support structures needed
- SLA: High-resolution, best for detailed models and smooth finishes
9. What are the key properties of PLA, ABS, and Nylon in AM applications?
- PLA: Biodegradable, brittle, low cost
- ABS: Impact-resistant, durable, requires a heated bed
- Nylon: Wear-resistant, suitable for functional parts
10. Why is Nylon 12 commonly used in SLS-based AM?
Nylon 12 offers high strength, fatigue resistance, and durability, making it ideal for functional prototypes and end-use parts.
11. What are the benefits of using high-temperature resins in SLA/DLP printing?
High-temperature resins provide thermal resistance and mechanical strength, suitable for applications exposed to heat and mechanical stress.
Metals in Additive Manufacturing
12. What are the most commonly used metals in AM, and what industries benefit from them?
- Titanium (Ti-6Al-4V): Aerospace, medical
- Stainless Steel (316L, 17-4 PH): Industrial, medical
- Aluminum (AlSi10Mg, 6061): Automotive, aerospace
- Inconel (625, 718): High-temperature applications (aerospace, energy)
13. What are the key properties of Titanium (Ti-6Al-4V) in AM applications?
Titanium is lightweight, biocompatible, and corrosion-resistant, making it ideal for aerospace and medical implants.
14. How does the thermal stress in metal AM impact part quality, and how can it be mitigated?
Thermal stress can cause warping and cracking. Solutions include heat treatment, optimized support structures, and controlled cooling.
15. Why are support structures necessary in metal AM, and how do they affect post-processing?
Supports prevent deformation during printing. However, they increase material use and require removal, which adds to post-processing costs.
Composite Materials in Additive Manufacturing
16. What advantages do composite materials offer over pure polymers in AM?
Composites enhance strength, stiffness, and durability by integrating reinforcing fibers such as carbon or glass into a polymer matrix. яндекс
17. How do continuous fiber-reinforced composites compare to chopped fiber-reinforced materials?
- Continuous fibers: Higher strength, directional reinforcement
- Chopped fibers: Easier processing, lower cost, isotropic properties
18. What are the applications of Carbon Fiber-Reinforced Polymers (CFRP) in AM?
CFRP is used in aerospace and automotive industries for lightweight, high-strength components.
19. What challenges arise from the thermal expansion properties of composite materials in AM?
Uneven thermal expansion can lead to warping and dimensional inaccuracies, requiring optimized print settings and material selection.
Cost & Production Considerations in AM
20. Why are AM materials typically more expensive per unit than traditional manufacturing materials?
AM materials, especially metals and resins, require specialized processing, which increases costs compared to bulk materials used in traditional methods.
21. How do layer height and print speed impact AM production costs?
Finer layers improve quality but increase print time and cost, whereas thicker layers reduce time but lower resolution.
22. What are the typical cost ranges for polymers, metals, and resins used in AM?
- Polymers: $50–$150/kg
- Metals: $300–$1,000/kg
- Resins: $100–$500/L
23. How does post-processing influence the total cost of an AM-produced part?
Processes such as support removal, polishing, and heat treatment add labor and material costs.
24. What are the key cost differences between AM, CNC machining, and injection molding?
- Injection Molding: Low per-part cost, high tooling investment
- CNC Machining: Cost varies by complexity
- AM: No tooling costs but higher per-unit costs for production
25. What types of production runs are most cost-effective for AM?
AM is best suited for low-to-medium production runs (1–10,000 parts), complex geometries, and on-demand manufacturing.
Strategies to Reduce AM Production Costs
26. How does topology optimization reduce material usage in AM?
It removes unnecessary material while maintaining structural integrity, reducing cost and print time.
27. What techniques can minimize the need for support structures in AM?
Using self-supporting geometries, optimal part orientation, and minimizing overhangs.
28. How does batching and nesting parts improve cost efficiency in AM?
Maximizing build volume utilization reduces per-part costs and production time.
29. What is hybrid manufacturing, and how does it optimize AM costs?
Combining AM with CNC machining allows for precise tolerances while minimizing AM material costs.
Industry-Specific Applications of AM
30. What are some notable AM applications in the aerospace, medical, and automotive industries?
- Aerospace: Lightweight brackets, fuel nozzles, satellite parts
- Medical: Custom implants, surgical models
- Automotive: 3D-printed brake calipers, battery cooling plates
Accelerate Your Additive Manufacturing with RapidMade
From rapid prototyping to full-scale production, RapidMade provides high-quality, cost-effective industrial 3D printing solutions. Our expertise in DfAM, material selection, and cost optimization ensures superior performance and efficiency.
📩 Get a quote today: www.rapidmade.com